Case Study: Soliculture Research Greenhouse
By Anna Richmond-Mueller, NCAT Energy Analyst
When it comes to conversations surrounding energy and water use in the modern world, the agricultural industry’s consumption of both is often at the forefront. As the world’s population continues to grow, humanity is tasked with the challenge of finding ways to meet both food and energy demands across the globe. “I really believe that greenhouse growing is the epitome of sustainable agriculture,” says Soliculture cofounder and CEO Dr. Glenn Alers. Whether it is the ability to greatly increase crop yields when compared to traditional open field growing, or the potential for increased water-use efficiency in combination with hydroponics, greenhouses could play a key role in addressing these concerns. Solar greenhouses also could also play a role in mitigating future energy crises.
Soliculture began in 2012 as a startup in the Physics Department at the University of California Santa Cruz. Dr. Alers and his cofounder were conducting research on luminescent solar concentrator panels when he realized the technology’s agricultural potential. Luminescent solar panels utilize a luminescent dye that selectively absorbs a portion of the solar spectrum and readmits light at a different wavelength. The dye used in Soliculture panels absorbs the green portion of sunlight with low photosynthesis efficiency and converts it to red light with much higher photosynthesis efficiency. The panels enhance the light quality inside a greenhouse by optimizing the light spectrum for improved plant growth. Moreover, the panels contain bifacial cells that collect the light reflected from the crops planted below them. The red luminescent dye also enhances the power output of embedded cells by 15 to 32%, compared to a conventional panel.
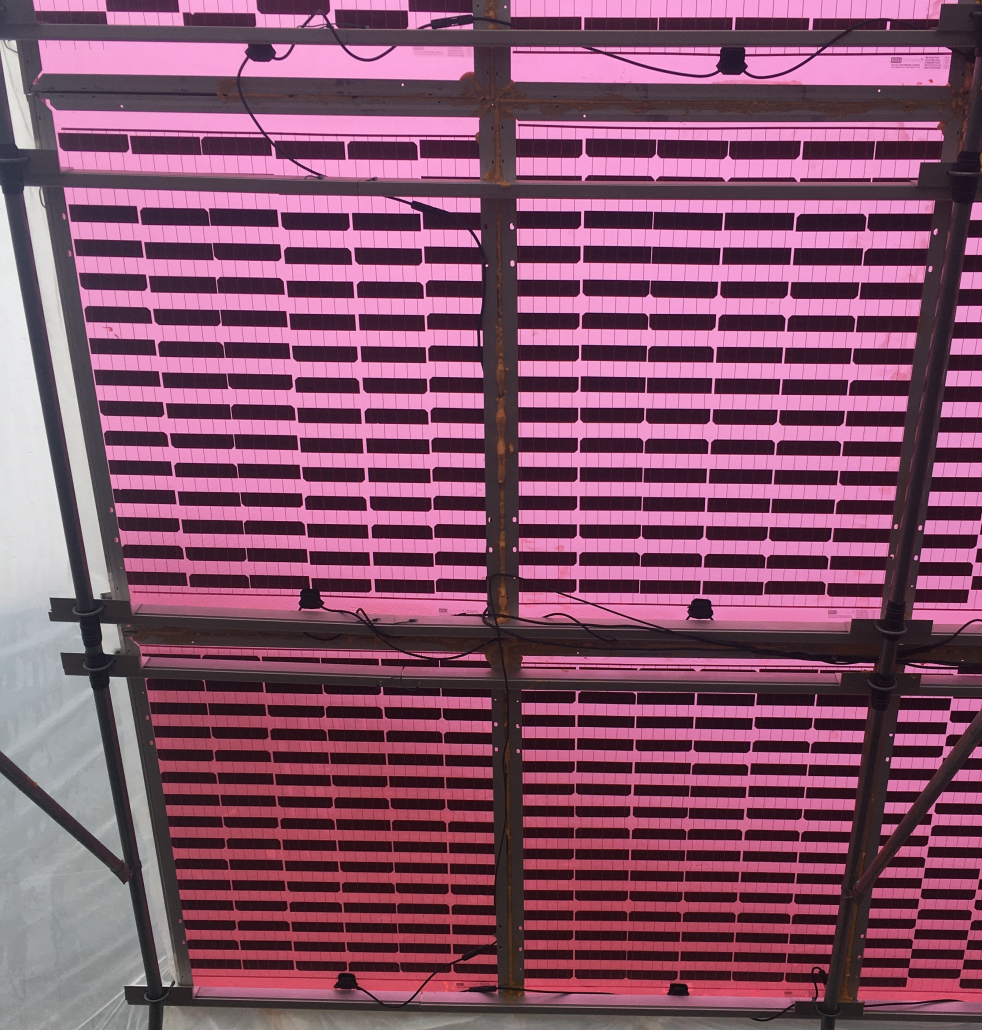
In 2019, Soliculture began a research project on Whiskey Hill Farms in Watsonville, California, aimed at developing these solar panels for use on hybrid high-tunnel greenhouses. As an active organic farm already growing produce in both field and greenhouse settings, Whiskey Hill Farms served as an ideal host for the project. The Soliculture research greenhouse was constructed from the ground up with help from a local high tunnel installer, measuring 120’ long and 25’ wide upon completion. Additional bracing was added to the roof structure, forming a “queen style” truss to support the weight of the panels. One half of the high tunnel was covered by a semi-clear plastic film that served as the control for the upcoming crop growth study, and the other was covered by Soliculture solar panels. These panels were specially designed for high tunnel greenhouses and had a cell coverage of 42%.
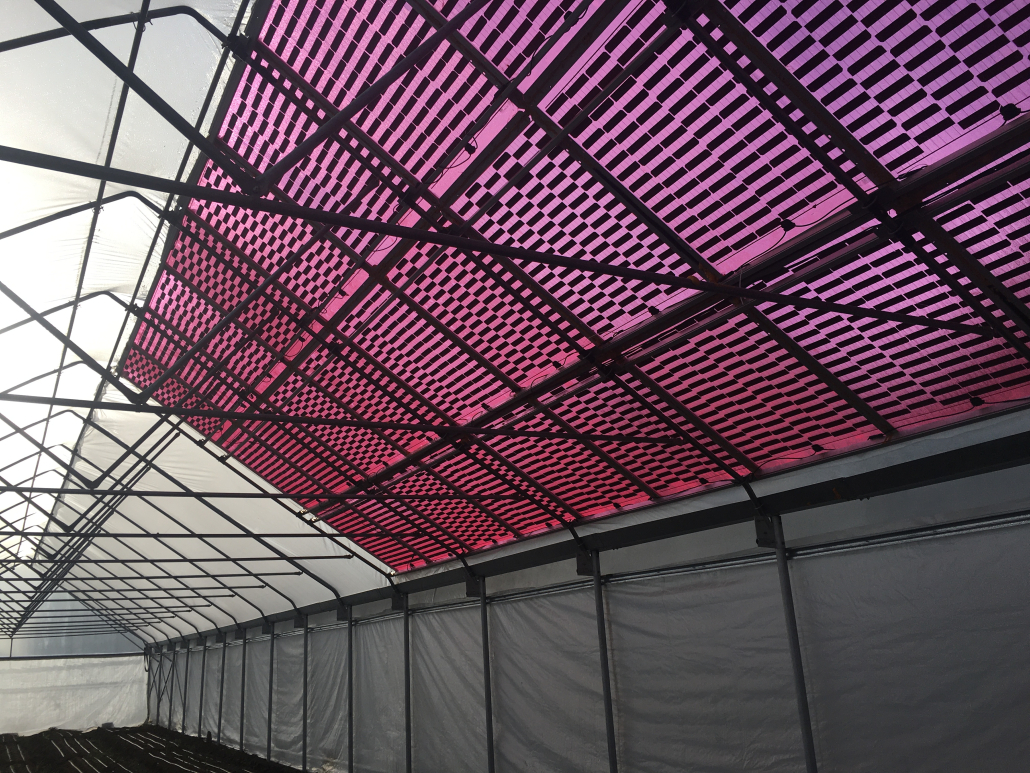
The project hit a temporary snag when waterproofing the panel racking system proved to be more of a challenge than expected. At first, horizontal mounting bars were attached to the tubing of the greenhouse’s roof frame and foam weather stripping was installed between the panels to create a watertight seal. Water was still able to leak through at the corners and where the mounting bolts connected the panels to the roof. Knowing the potential for these leaks to cause erosion and negatively impact crop growth, the Soliculture team returned to their laboratory and created a modified racking system specifically for high tunnel application. This new system used mounting brackets that attached to the bottom of the frame and utilized a rubber “T” gasket inserted between the panels to create a seal. Finally, the plastic film portion of the roof was attached to the panels using an aluminum channel screwed into the panel frame and “wiggle wire” to hold the plastic film in position. With a waterproof roof in place, the crop trail was ready to commence.
The following crops were selected for planting following the completion of the high tunnel in mid-November: strawberries, red romaine lettuce, red butter head lettuce, cilantro, mustard greens, and turmeric. To ensure the trial’s results would translate to commercial production, the research team used common commercial growing methods throughout the duration of the trial. These methods included drip irrigation with untreated well water, sand filtration, and liquid organic fertigation. By the end of the trial, the majority of the crops grown under Soliculture panels matured close to two weeks ahead of those grown under the clear film portion of the high tunnel. The fresh weight for the under-panel crops was superior as well, with red butter head lettuce seeing the greatest benefit at 145% higher weight. Mustard greens weighed in at 95% higher, cilantro at 35%, romaine lettuce at 32%, and turmeric at 25%. The strawberry fruit showed no statistically significant difference in fresh weight, but the single 5’ by 120’ planted bed yielded more than 350 pounds of fruit by the end of July.
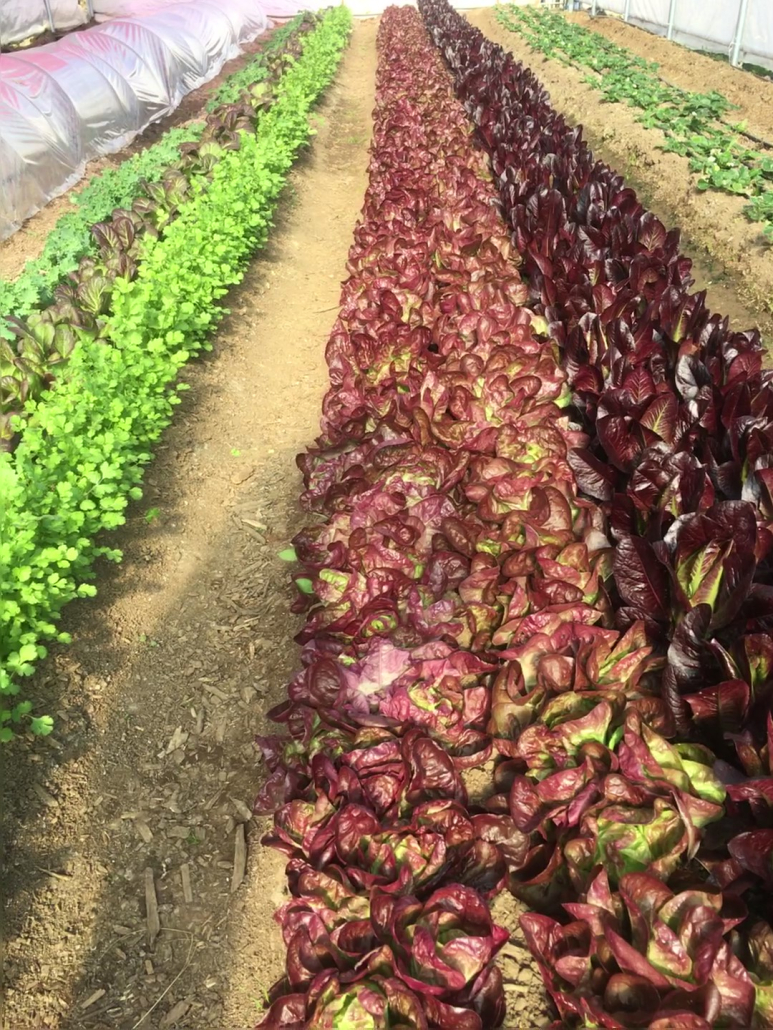
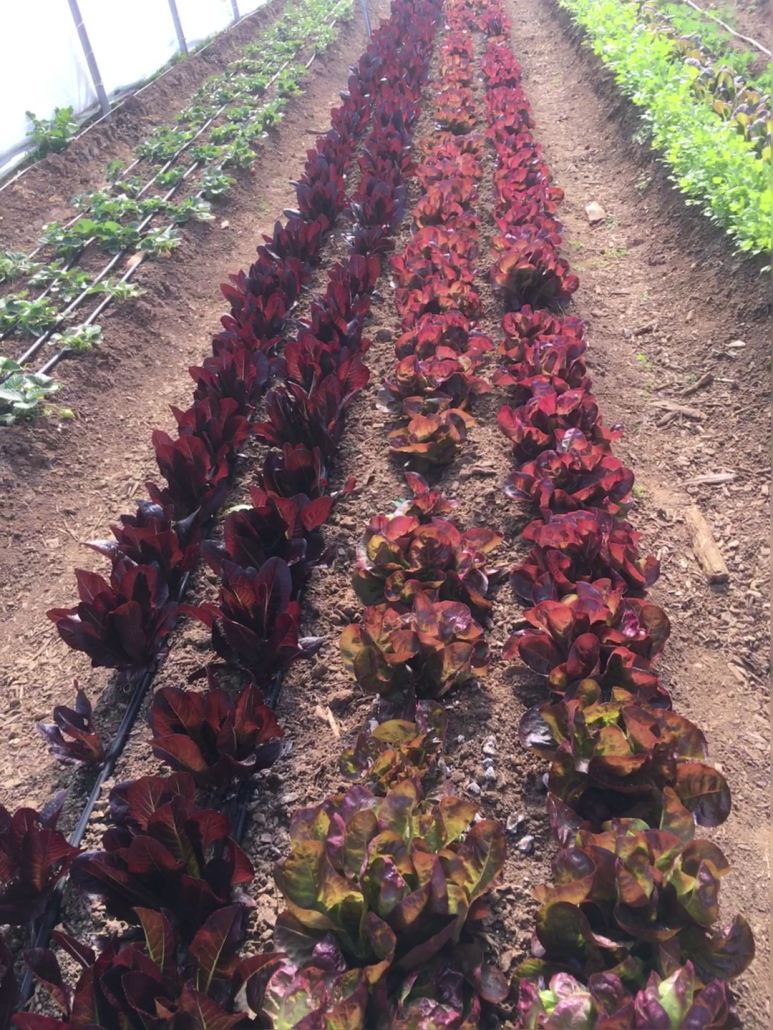
On top of the very successful crop trial, the power generated by the greenhouse panels was used by Whiskey Hill Farms to power their day-to-day operations. A total of 58 Soliculture panels provided the farm with a 6kW system, which was connected to an inverter. The AC power was then fed back into the farm’s power system, a testament to how greenhouse solar can benefit the farm beyond improving plant growth.
The field of agrivoltaics is constantly evolving, with numerous researchers and farmers searching for the ideal nexus between the agricultural industry and energy production. Soliculture’s contributions to agrivoltaics is important for farmers who have reservations about growing food underneath and around solar panels. “We haven’t seen any negative effect on plant growth,” Dr. Alers says, referring to the Whiskey Hill Farms project and several other successful Soliculture installations across the United States and Canada. Greenhouse production has always had the potential to help alleviate the water crisis and increase the amount of food grown per acre, but Soliculture’s technology is giving it a bright future in energy production, as well.
All photos courtesy of Soliculture